Navigating the FDA Certification Process and Costs for Paper Bowls
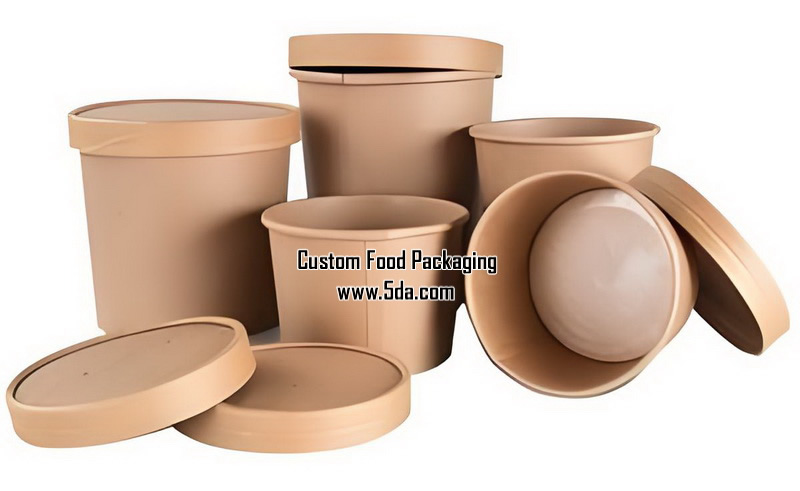
Exporting paper bowls to the United States requires a critical step in the production process: obtaining Food and Drug Administration (FDA) certification. This ensures that your paper bowls comply with the rigorous safety standards set by the FDA for food contact materials. In this article, we'll outline the comprehensive FDA certification process for paper bowls, including the steps involved and an overview of associated costs.
FDA Certification Process for Paper Bowls
1. Understanding FDA Regulations
Before embarking on the certification journey, it's essential to familiarize yourself with FDA regulations relevant to paper bowls. The primary guidance document is the FDA's Code of Federal Regulations (CFR) Title 21, which outlines the standards for food contact materials. Additionally, you'll need to understand the agency's stance on chemicals and additives used in the production of paper bowls.2. Consulting with an Expert
Given the complexity of FDA regulations, it's highly recommended to consult with an FDA consultant or regulatory affairs expert. They can provide guidance on the specific requirements for your product, recommend necessary tests, and help streamline the application process.3. Gathering Documentation
Prepare a comprehensive set of documents, including:Product Information Sheet: Detailing the materials used, manufacturing process, and intended use of the paper bowls.
Material Safety Data Sheets (MSDS): For all chemicals and additives used in production.
Technical Specifications: Outlining the physical and chemical properties of the paper bowls.
Quality Control Procedures: Documenting your in-house quality checks and assurance measures.
4. Pre-Submission Consultation (Optional)
While not mandatory, the FDA offers pre-submission consultations where you can discuss your product and its compliance strategy with FDA staff. This can help identify potential issues before formal submission.5. Submission of Application and Testing Samples
Submit your application to the FDA, along with representative samples of your paper bowls. The application should include all the required documentation and specify the necessary tests, such as:Chloroform-Soluble Extractives Test: Evaluating the leachables in water, 8% alcohol, 50% alcohol, and n-heptane.
Migration Testing: Measuring the amount of substances that migrate from the paper bowls into food simulants.
Microbiological Testing: Ensuring the absence of harmful microorganisms.
6. FDA Review
The FDA will review your application and test results. This process can take several months, depending on the complexity of your product and the current workload of the agency.7. Post-Approval Monitoring
Once your paper bowls receive FDA clearance, you'll need to maintain compliance through regular quality control checks and prompt reporting of any changes to the product or its manufacturing process.FDA Certification Costs
The cost of FDA certification for paper bowls varies widely and depends on several factors, including:Product Complexity: The more complex the materials and production process, the more extensive the testing and documentation required.
Testing Fees: Fees charged by accredited laboratories for conducting the necessary tests. These can range from a few thousand to tens of thousands of dollars, depending on the number and type of tests required.
Consulting Fees: Costs associated with hiring an FDA consultant or regulatory affairs expert.
Application Fees: While there are no direct application fees for FDA clearance, the costs of preparing and submitting the application can be significant. It's important to note that these costs are investments in your product's compliance and access to the US market. While they may seem daunting, they ultimately pave the way for your paper bowls to reach consumers with confidence and trust.