Navigating the FDA Certification for Paper Cups
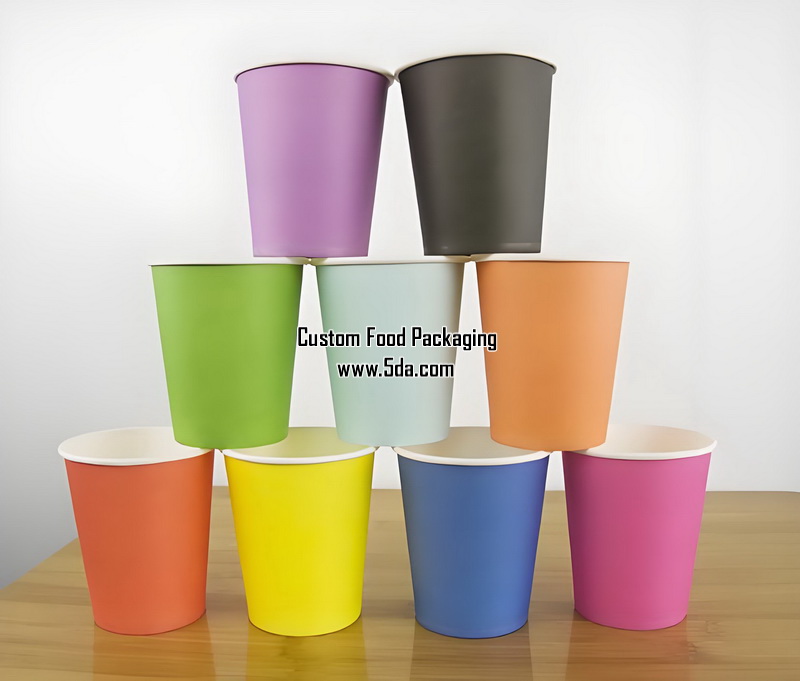
Entering the US market with paper cups requires a crucial step: securing Food and Drug Administration (FDA) certification. This process ensures that your paper cups meet the stringent safety standards set by the FDA for food contact materials, earning the trust of consumers and retailers alike.
Understanding the Importance of FDA Certification
FDA certification is not just a formality; it's a seal of approval that verifies the safety and quality of your paper cups. With this certification, you can confidently market your products to the vast US market, knowing that they comply with the highest regulatory standards.
Key Steps in the FDA Certification Process
1. Familiarize Yourself with FDA Regulations
Start by studying the FDA's Code of Federal Regulations (CFR) Title 21, particularly the sections related to food contact materials. Understand the agency's requirements for paper cups, including materials used, manufacturing processes, and intended use.
2. Consult with an Expert
Given the intricacies of FDA regulations, engage an FDA consultant or regulatory affairs expert. They can guide you through the certification process, recommend necessary tests, and ensure your product meets all the requirements.
3. Prepare Documentation
Compile a comprehensive set of documents, including product information sheets, material safety data sheets (MSDS), technical specifications, and quality control procedures. These documents will form the backbone of your application.
4. Submit an Application and Samples
Once ready, submit your application to the FDA along with representative samples of your paper cups. Specify the necessary tests, such as migration testing and microbiological analysis, to ensure your product is safe for food contact.
5. Wait for FDA Review and Approval
The FDA will thoroughly review your application and test results. This process can take several months, depending on the complexity of your product and the agency's workload. Remain in communication with the FDA during this time to address any queries or concerns.
Costs Associated with FDA Certification
The cost of FDA certification for paper cups varies depending on several factors:
- Product Complexity: More complex products require more extensive testing and documentation.
- Testing Fees: Fees charged by accredited laboratories for conducting necessary tests.
- Consulting Fees: Costs associated with hiring an FDA consultant or regulatory affairs expert.
- Application Preparation: Time and resources invested in preparing and submitting the application.
While these costs may seem significant, they are essential investments in your product's compliance and market access. Remember, FDA certification is a testament to your commitment to safety and quality.
Maintaining Compliance
Once your paper cups receive FDA certification, you must maintain compliance through regular quality control checks and prompt reporting of any changes to the product or its manufacturing process. The FDA may also conduct unannounced inspections to ensure continued compliance.
By navigating the FDA certification process with diligence and expertise, you can confidently bring your paper cups to the US market, knowing that they meet the highest standards for safety and quality.